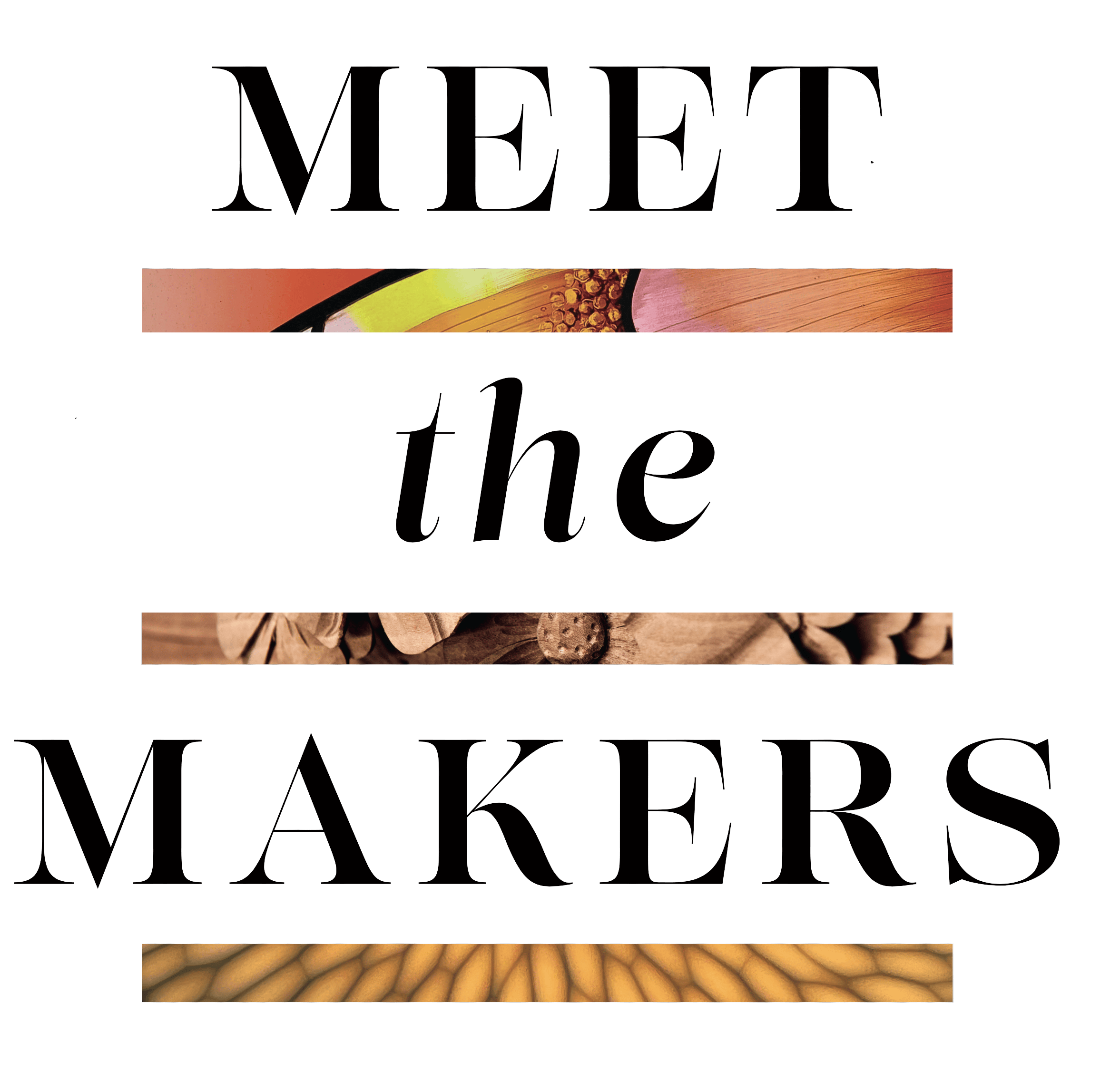
The artisans working at the highest level of their craft
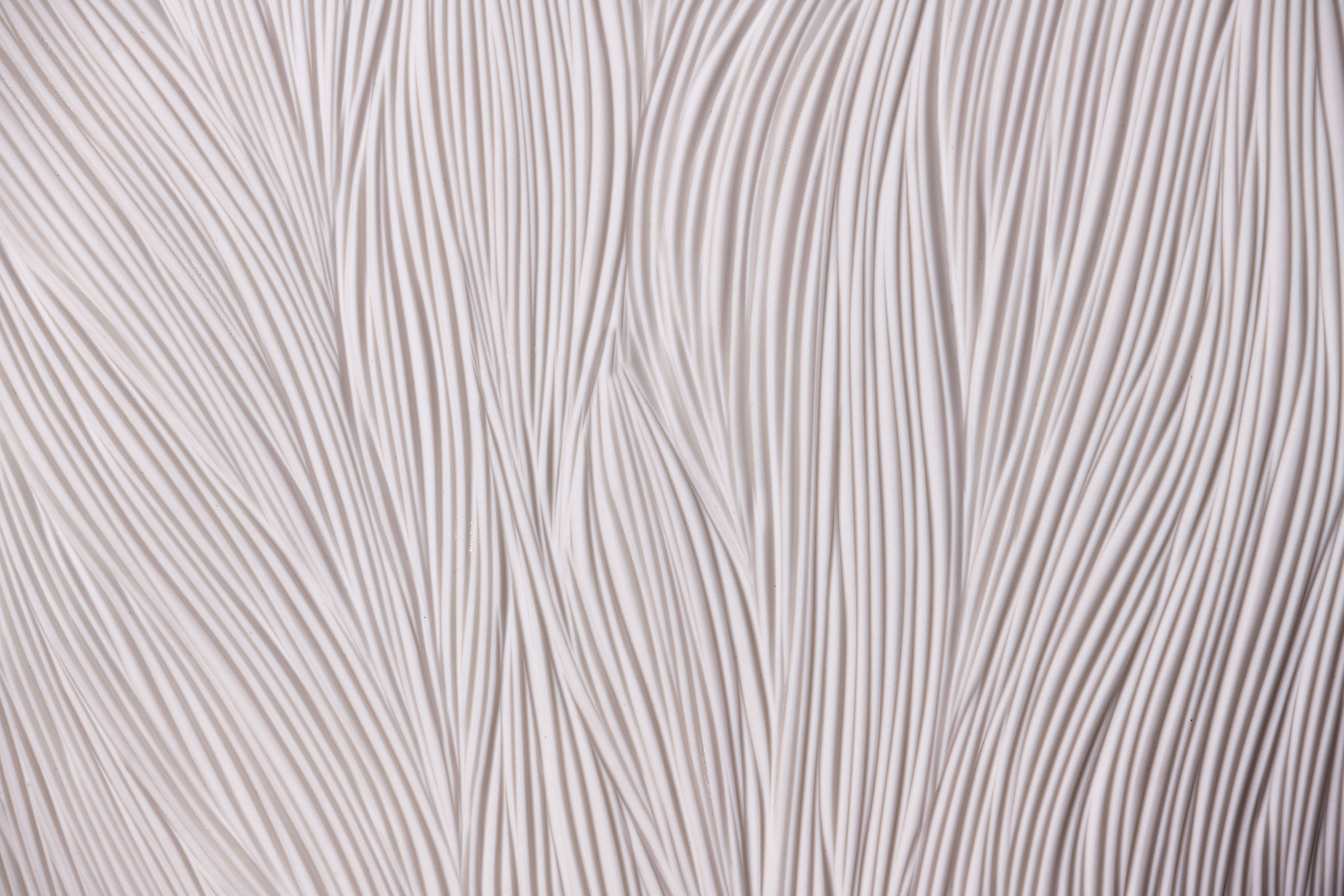
WINCH DESIGN
Charlotte Hogarth-Jones meets the winners of the inaugural BOAT Artistry & Craft Awards and finds out just what it takes to bring beauty to the world’s best boats
CRISTINA VEZZINI & SHENG TSANG CHEN
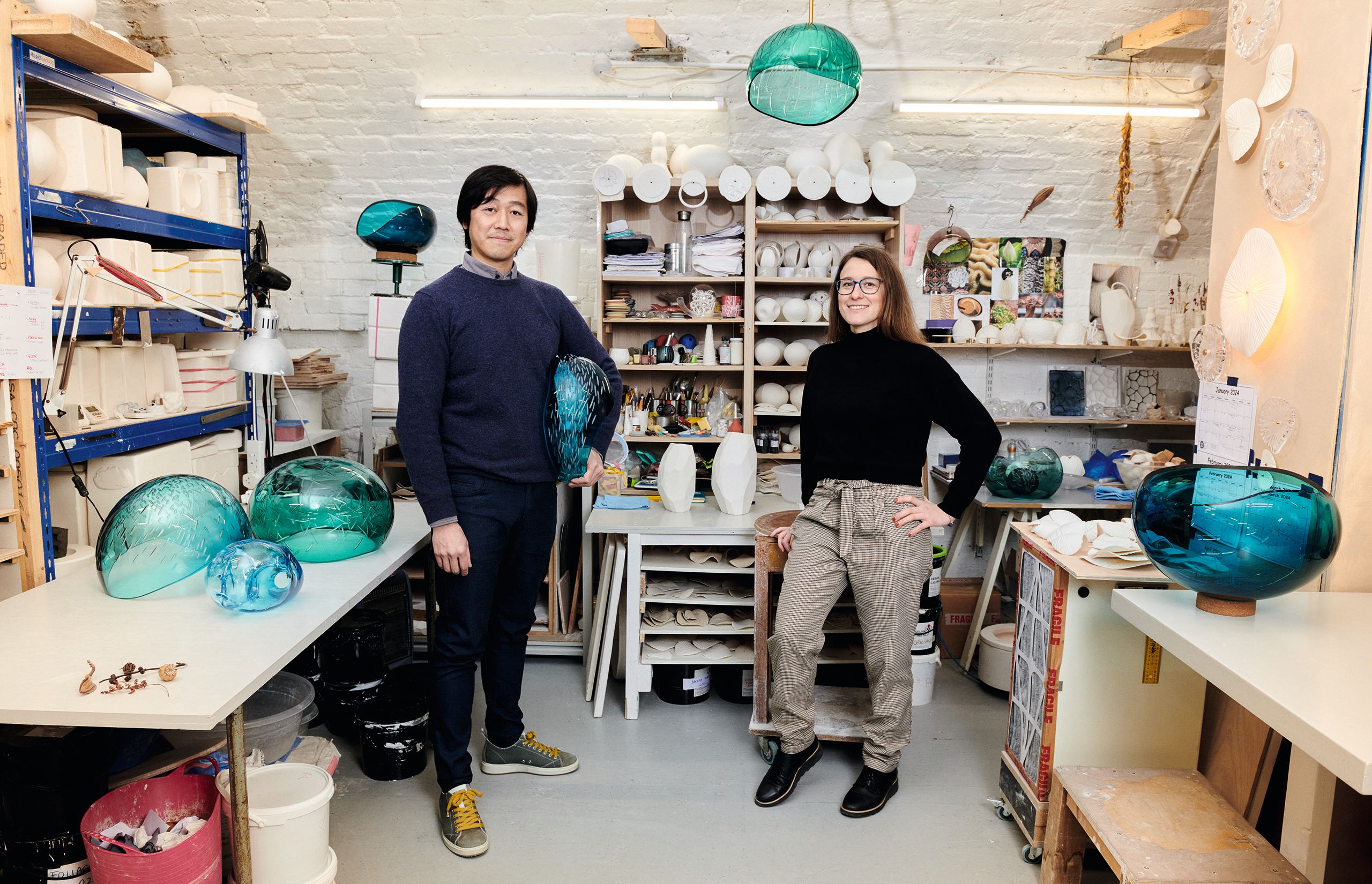
Award: Excellence in Craftsmanship
Nominated by: Winch Design
For: Sculptural light fitting on board 70-metre Amoa
It’s a good job that Cristina Vezzini and Sheng Tsang Chen (also known as Stan) are both patient. Their work – which involves delicate, paper-thin porcelain pieces, often coupled with glass spheres or plates – would test even the most experienced maker.
“Those two materials are particularly tricky to combine because they can’t be fused together,” explains Chen. “They expand at different rates during the heating process, which can cause the glass to crack, so they have to be made separately to fit each other. We always say it’s a conversation between the material and ourselves, and our method is to design through making.”
What this means in practice is that the pair travel from their studio in Haggerston, east London, to a glass-blowing studio in Trowbridge, near Bath, several times a month, to explore preliminary ideas and see how the glass flows and sets during the process.
Back in the studio they use these models to refine their ideas, until they are able to create a piece that is formed naturally, but in line with their designs.
Some works take years to finalise. Their studio is littered with unusual and beautiful pieces of glass, piled high, all waiting to find their perfect porcelain match – or for the right project to come along.
“You have to leave time for ideas to develop,” they say. The finishing touch to all of their pieces is light. It complements the transparency of the glass and the warmth of the ceramics, and allows their installations to take on a different life when darkness falls.
“We're always intrigued by how the light shines through water and onto the sea floor”
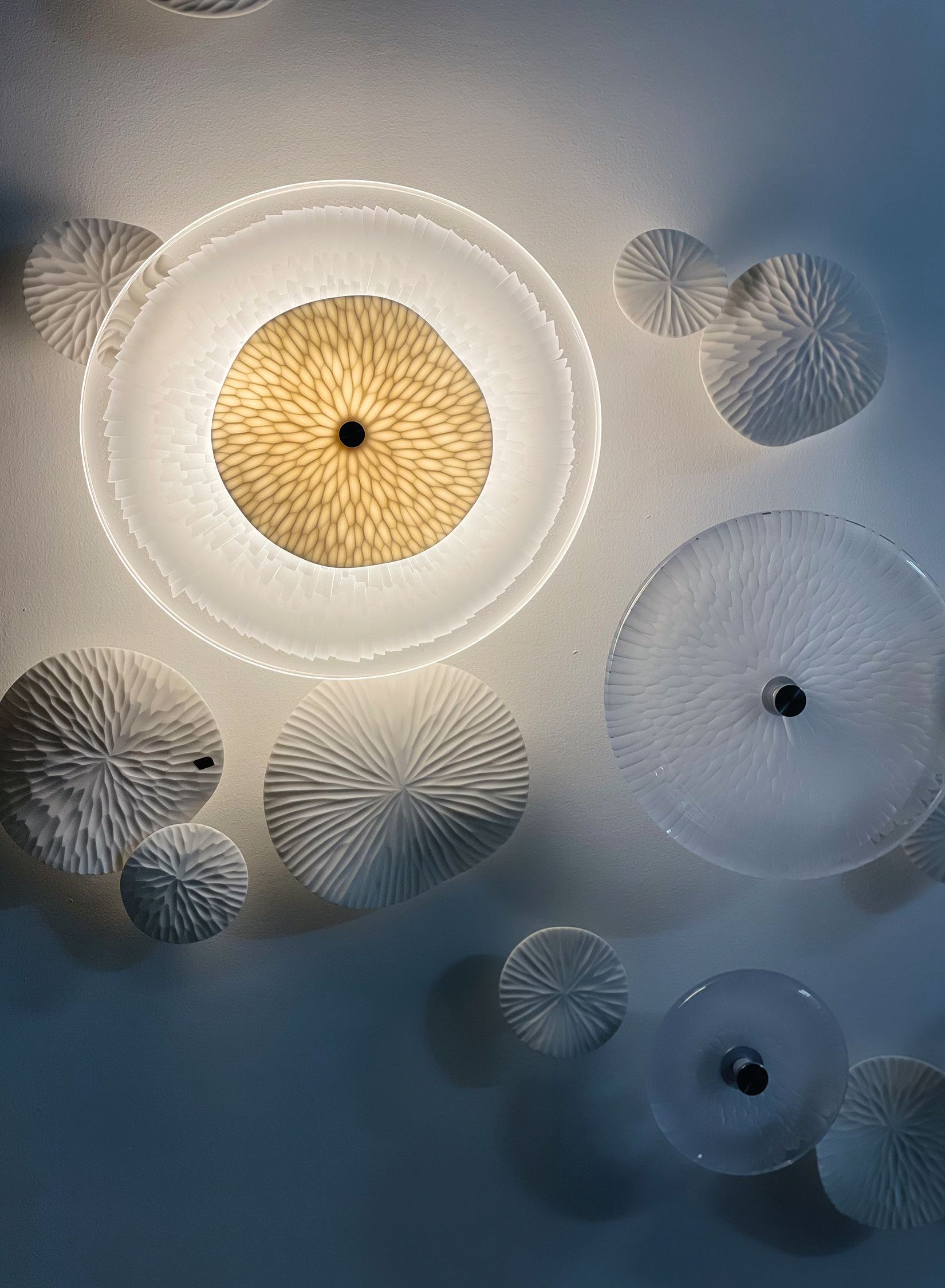
Of course, you’d be forgiven for thinking glass and porcelain aren’t the best materials for the high seas, yet the duo are a natural fit for the superyacht industry.
“We’re both scuba divers, so we’re intrigued by how the light shines through water and onto the sea floor, and you see a lot of texture in our work that’s inspired by nature – sometimes plants but also marine life like sea urchins and coral,” explains Vezzini.
She also collects seeds and seed pods from around the world, and often uses them as the basis of her designs. “My parents are doctors and last Christmas they bought me my favourite present – a microscope!” she laughs, “I like looking at all these things up close so that I can see their patterns.”
Their winning BACA piece was a commission for Winch Design for 70-metre Amoa, a wall installation behind a staircase that represented water and sand. The glass was transparent, with lots of textures inspired by corals, while the porcelain represented the sand.
Made up of discs ranging from 10 to 35 centimetres, and including seven lights (both ceramic and glass), each disc was secured “like a sandwich”, with a metal fitting in front and behind it that clamped it tightly together and protected it from movement.
Working together for 11 years, Chen came to the UK from Taiwan to study glass blowing, training under glass master Rob Marshall before completing a further qualification at the Royal College of Art, where he met Vezzini. She was completing an MA in ceramics and glass, having received a BA in applied arts, and was producing work using wood, resin and porcelain at the time.
“Stan really helped me with the glass as I had no skills in working with this material,” she says. “What a lot of people don’t understand is that we’re not just the designers of our pieces, we’re the makers too,” says Chen. In an era of digitizing design and using AI software to progress ideas, “we’re losing this craft” of making, he explains. vezziniandchen.com
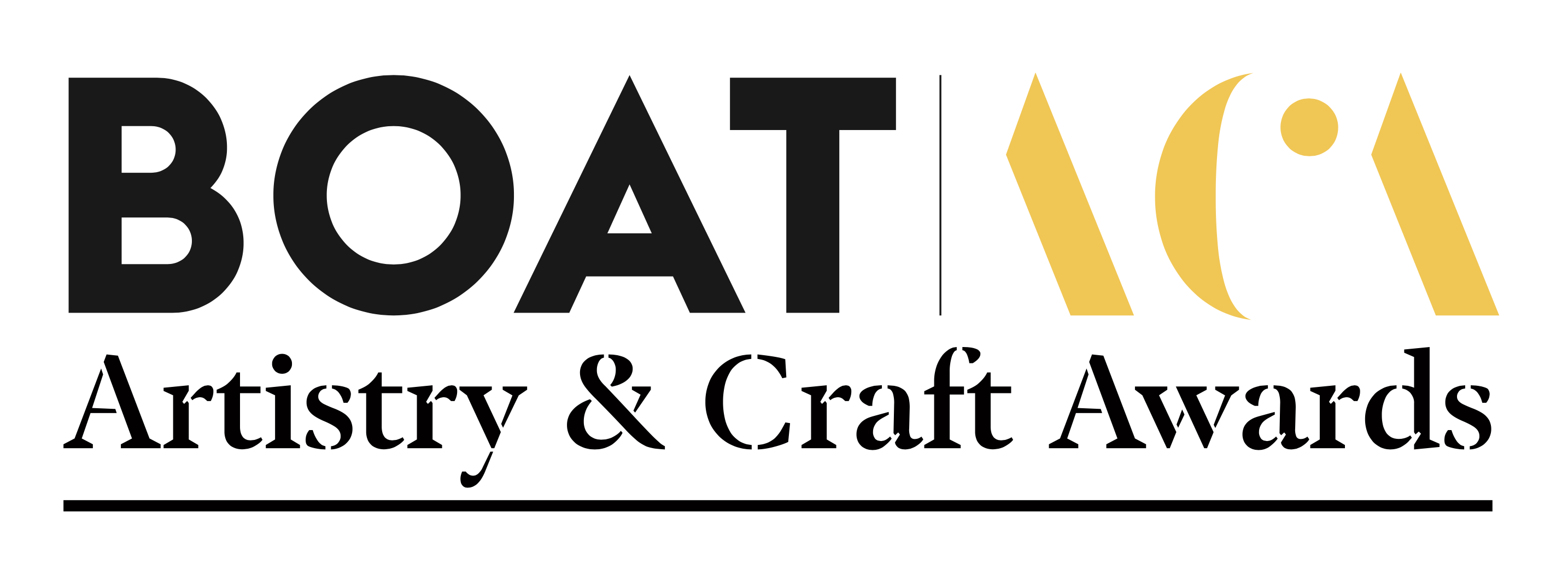
Have you commissioned or created something beautiful for a superyacht that’s launching this year? If so, we want to hear from you. Apply for the 2025 awards directly via the link below, or if you’re concerned about an NDA, or need support from a designer but don’t have direct access to them, please email ciara.hutchison@boatinternationalmedia.com for assistance.
GRACE AYSON
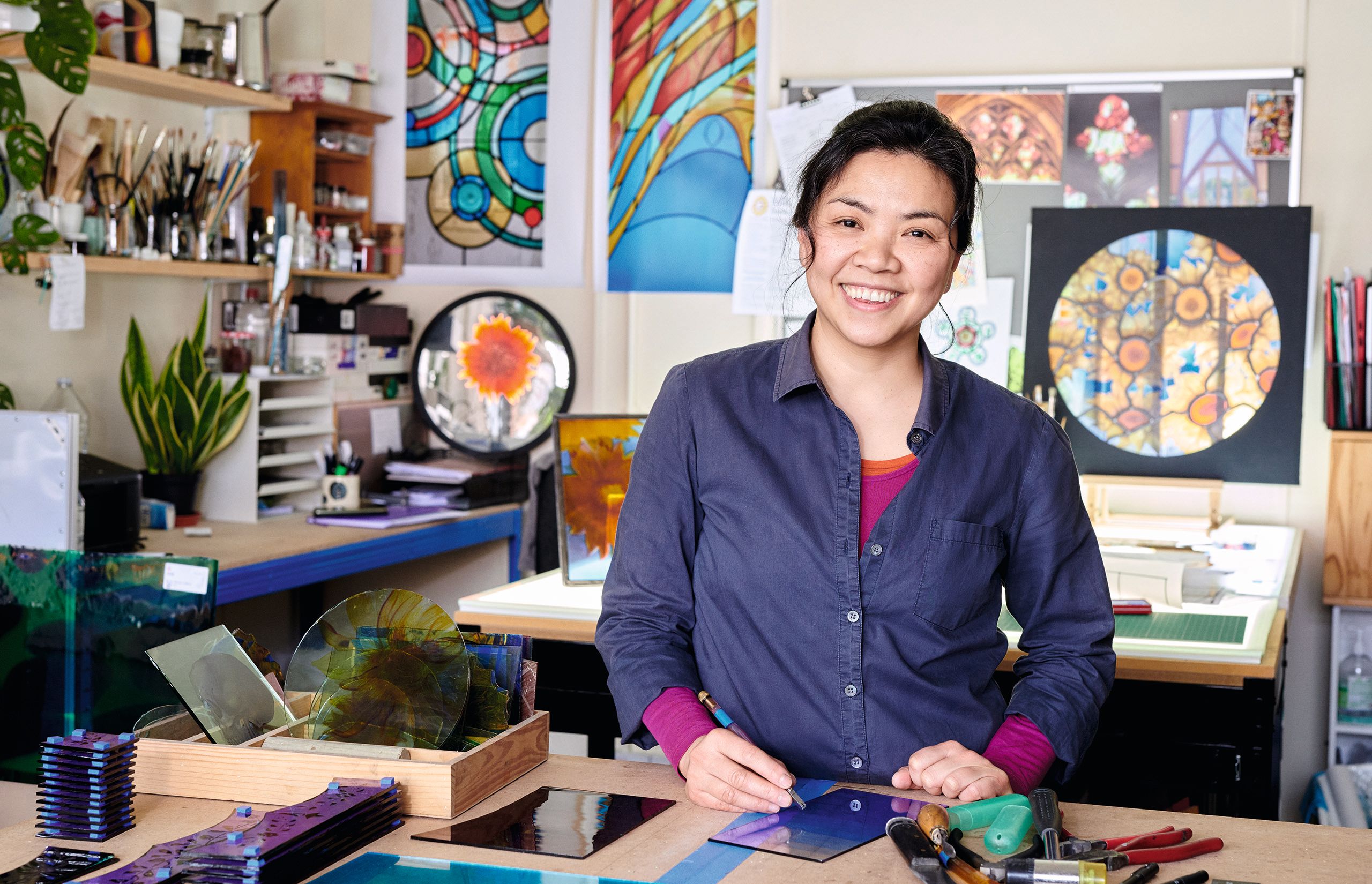
Award: Emerging Artisan of the Year
Nominated by: Bannenberg & Rowell
For: The Four Seasons stained-glass triptych on board 112-metre Renaissance
Stained-glass artisan Grace Ayson began her career as a sculptor. Working in grand houses and at monuments, she used to marvel at the coloured glass in the buildings she worked in.
“I loved how the atmosphere of the space changed continually as the sun moved throughout the day,” she recalls. “Then one day I saw the Marc Chagall windows in a little chapel in Tudeley, and I really liked them.
He was a painter, and they’re very contemporary.” They made her realise that she could combine her love of making with her more artistic talents. It wasn’t long before she was working on the windows of Canterbury Cathedral, not to mention private homes, institutional buildings and more.
Clients come to her with a brief initially. “Sometimes something immediately comes to mind for a design, and then I do lots of research, look at different sources, some of my own work... but in the end I always go back to that instinctual first thought,” she smiles.
Once her design is approved, she draws it out at full scale, known as a cartoon, and decides the cut line – where the glass will be cut and broken up and the lead lines will be.
She then selects the glass. “I always try to use mouth-blown, handmade glass, and sadly they just don’t make it in the UK anymore – it’s on the red list of endangered crafts,” she says.
Instead, she uses a company in Germany called LambertsGlas, where each sheet is blown by hand, with colours made to order. “It glitters and glows and refracts the light differently,” she explains.
Each glass piece is hand-painted according to the design, with some areas acid etched to create variations of texture and colour on some glass types, and enamels and silver stain are also applied to the surface.
The glass is then kiln-fired at a high temperature to fuse the paint, enamel and silver stains onto the glass surface permanently, before it is assembled with lead and soldered for stability and strength. “So many different processes go into every project – a whole skill set of techniques is needed,” she explains.
Ayson likes to push herself creatively. “When I got the yacht project, I thought, wow! This is great. It’s a new challenge – but it’s one I’m going to take.” Dickie Bannenberg of Bannenberg & Rowell initially didn’t disclose that the work was for a yacht. “At first he just asked if I was interested in making some large, backlit panels,” she recalls.
“When I got the yacht project, I thought, wow! It's a new challenge, but one I am going to take”
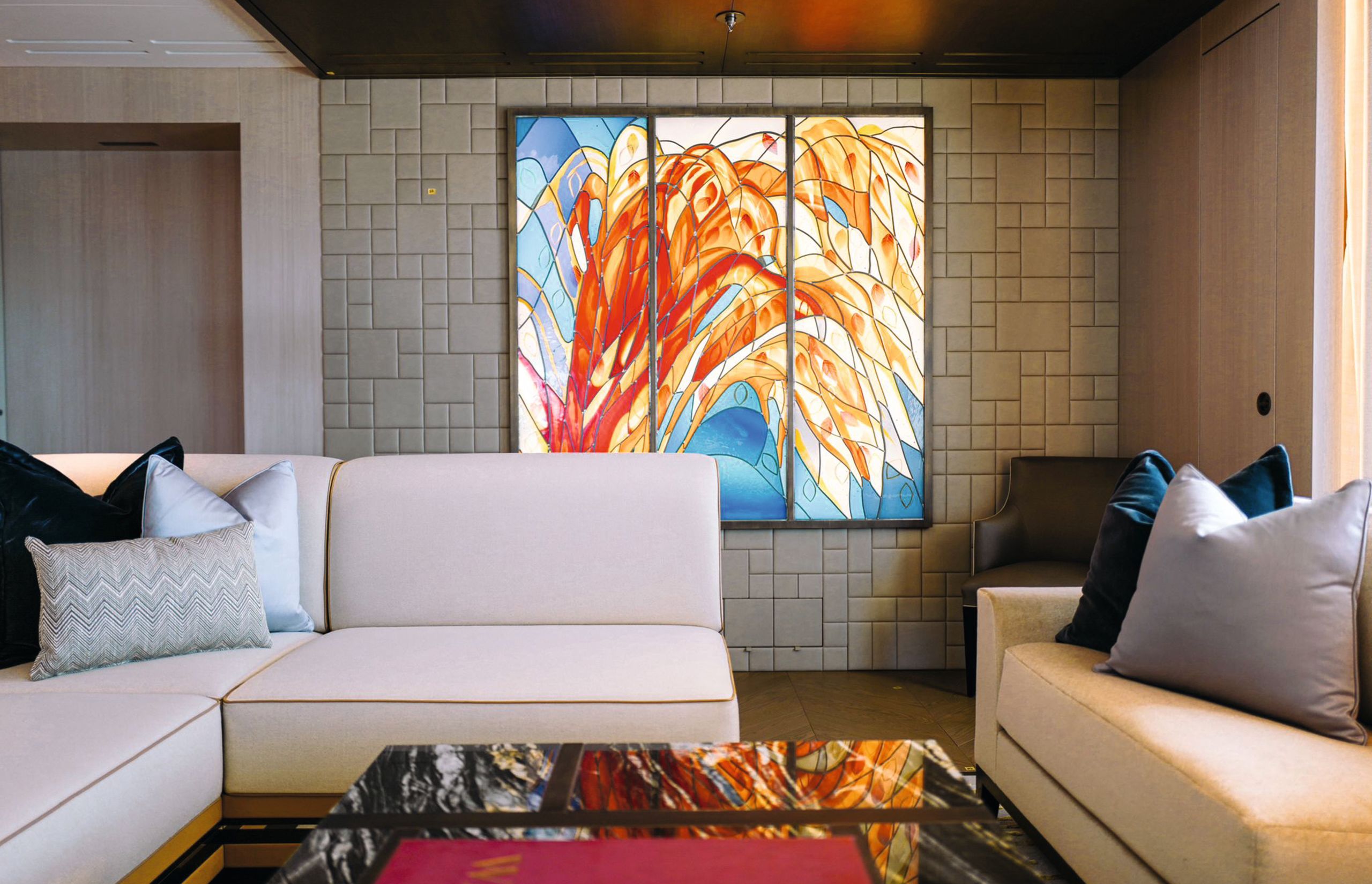
The challenge of the project was that it was to be artificially lit. “When you display stained glass in artificial light, it can flatten it – removing any movement or variations in the glass itself – so the choice of glass and painting technique was crucial,” she says. “Each sheet was chosen individually to work well with the artificial light.”
It was fortunate that she was able to liaise with Renaissance’s owners directly for the brief, a couple with a great love and appreciation of art.
“They really liked John Piper’s Green Man print series based on the four seasons, and they wanted the stained-glass panels to be based on these initially, but once I had begun designing they were happy for me to create what I thought would work. I created four different sets of watercolour designs and they chose one of them almost immediately.”
The Four Seasons is made of 160-square-centimetre panels, made in three sections to echo the design of the saloon’s wall dividers. The project took Ayson 10 months to complete, and was created entirely by herself. “I miss all the colours and glass that filled my studio while I was making them!” she says. “Plus Dickie and the team at Bannenberg & Rowell were lovely to work with.”
Ayson found her love of accuracy made her at home in the yachting world, working to a 2mm tolerance in all of her planning, and she was relieved when Bannenberg turned down her offer of encapsulating the panels in a protective casing. “He really wanted people to see the materials.”
Ayson sees great possibilities for stained glass on board yachts. As she points out, glass doesn’t have to be used for windows – it can be a focal point or blend into a design, used as room dividers or in spas.
One of the nicest things about working in glass, she goes on, is its longevity. Treated properly it can last for hundreds of years. “I love knowing that whether it’s something I’ve restored or made, there’s a little bit of me there that will be there for centuries – and that’s really special.” graceayson.com
PAUL JEWBY
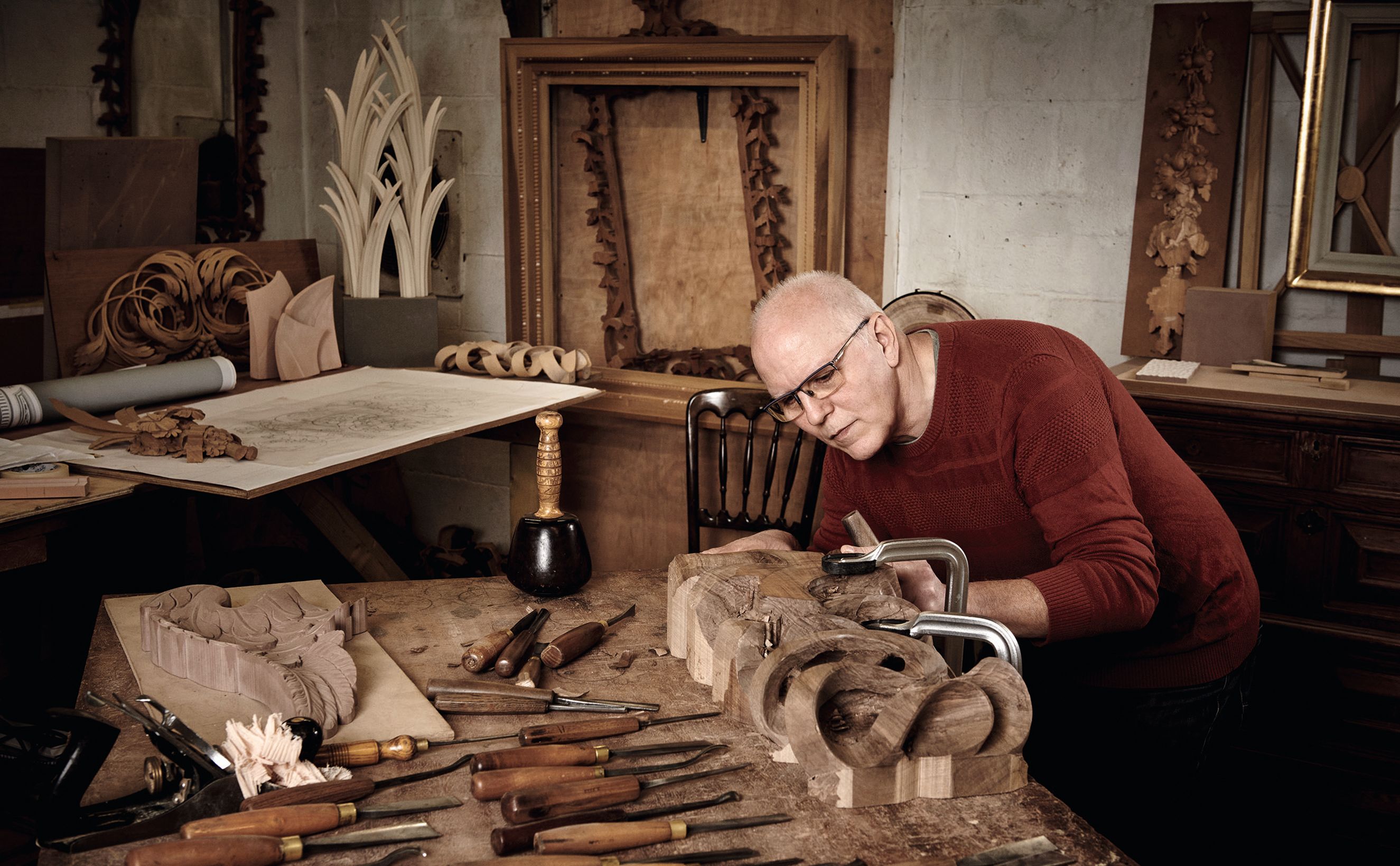
Judges’ special award
Nominated by: Winch Design
For: hand-carved oak panels on board 70-metre Amoa
Paul Jewby has been a professional wood carver for more than 40 years. But, he explains, his love of carving began many years beforehand. “When I was about five my mum bought me a tool set, and she could leave me in the garden all day with a couple of bits of wood and some nails and screws,” he recalls fondly. “She wouldn’t hear a peep out of me.”
At school he applied for cabinetmaking apprenticeships, but having received no replies to any of his letters, he eventually embarked on a carpentry and joinery apprenticeship aged 19.
“One day I got a reply saying, ‘We’ve lost your letter in our filing system, there’s an opportunity here for a woodcarver,’” but it was too late – Jewby was already six months into his carpentry apprenticeship, and “already getting bored of it”. He felt it was right to stay and finish, however, and the training became a strong foundation for the rest of his career.
A friend’s mother who taught history of art then began fuelling his interest for architectural ornament, and he soon went on to do an evening carving class, where the teacher urged him to apply for a full-time, two-year course at the City and Guilds London Art School.
Here, a lecturer described him as “a natural-born woodcarver”. “I have to say, I’ve always had this affinity with it, I’ve never seen myself doing anything else,” he admits. Looking at his work, it’s immediately apparent that there’s more to his skill than simply good training.
“To learn what to do, what to cut,
what forms to shape, that takes decades”
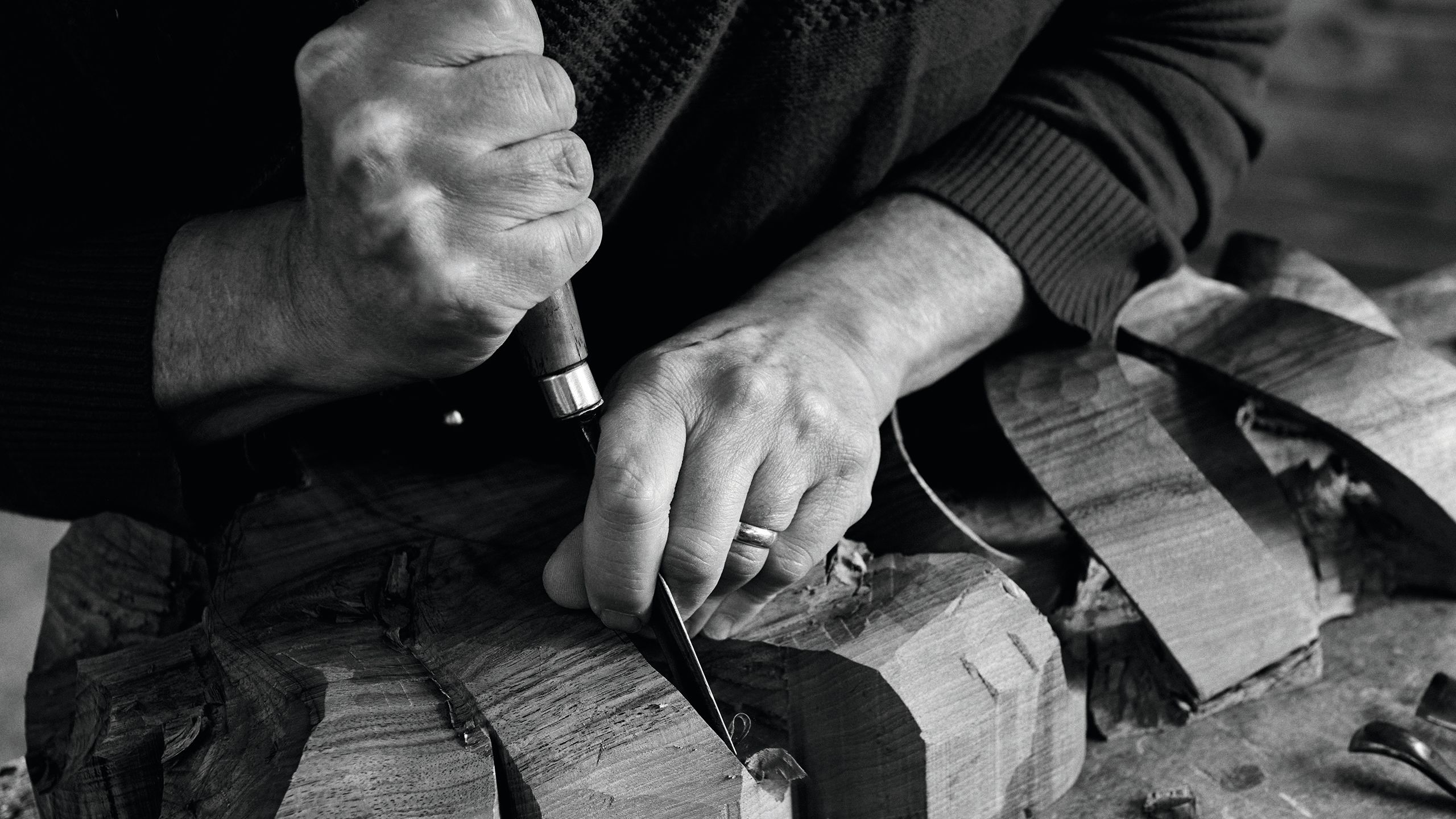
Jewby’s first official job was working for a company in London that restored fine 18th-century English furniture, supplying Partridge Fine Arts of Bond Street among others.
“It was the best that money could buy,” he recalls. “Giltwood, Chippendale, Adam, and you learned about different styles [of carving]... but then after 9/11, the antique trade in London died a death. It was fuelled by Americans coming over and buying, and they just stopped flying.”
Many of the older antique dealers were on the cusp of retirement anyway, so it was fortuitous for Jewby that just as many began to shut up shop, Winch Design approached him to do some work on a superyacht. “As soon as I met them, I thought, ‘This is where I want to be,’” he remembers. “It has snowballed ever since.”
Today, he works for numerous yacht designers and builders, as well as with architects and on other bespoke projects. “A lot of the time [people] have a concept and they’re pretty fixed on it,” he says.
The art of carving, however, is translating a 3D picture into what will work best with the medium. “As you’re working on something, you always change your mind a little bit, or you decide, actually, if I just do it slightly like this it’ll be better – so the work develops,” he explains.
One of his early works for Winch was for 62-metre Sea Owl, the 11-metre-high, three- metre-wide Tree of Life that he believes is “probably the single biggest carving done in a couple of hundred years”, and is incredibly proud of.
His BACA commendation, meanwhile, was for a series of carved wooden panels that formed 12 doors on board Amoa – a challenging physical task as the oak was kiln dried to such a degree that “there’s very little give in the tool – you really have to push it”, he explains. It was back-breaking too – long days were spent leaning right over the wide panels in order to work on the centre.
The whole project took two years to develop, with Jewby largely working alone. Each panel took two weeks as a minimum to make – some took closer to five – and the fact that the oak was made up of numerous strips added an extra element of complexity to the job. “You’ve got the grain of one strip running one way and the other grain running another way. So you get a rip in the grain which is challenging to carve,” he explains.
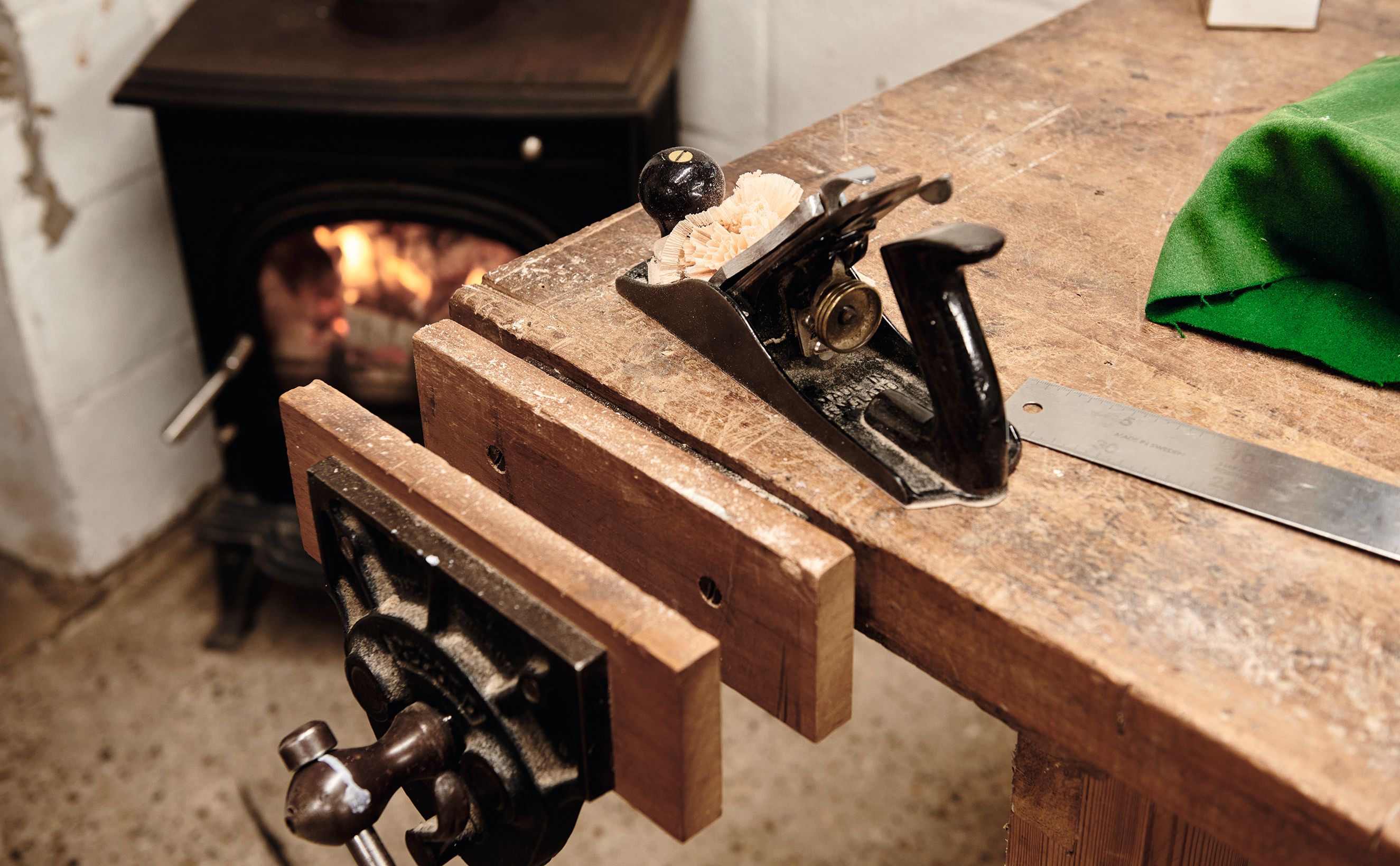
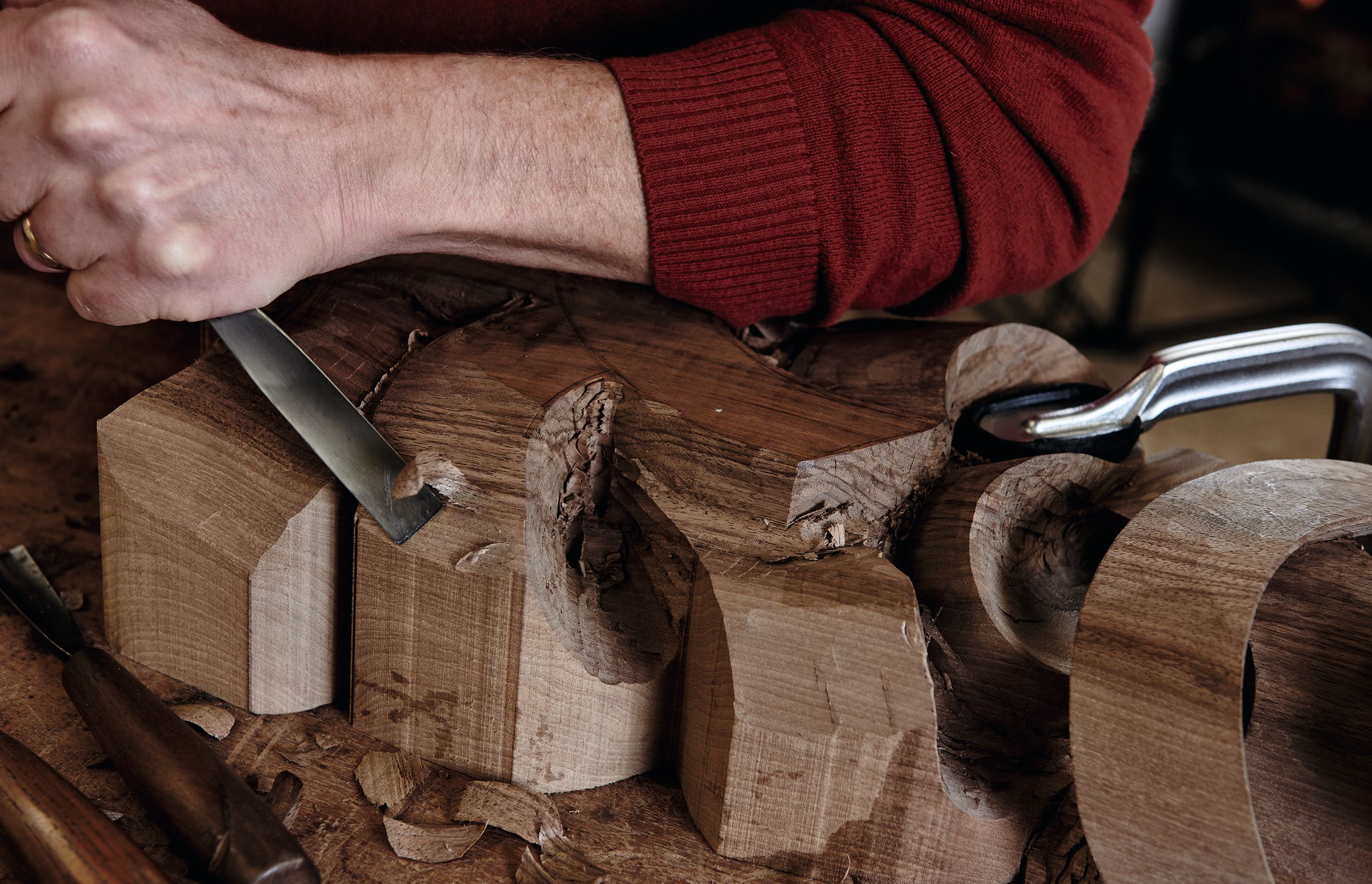
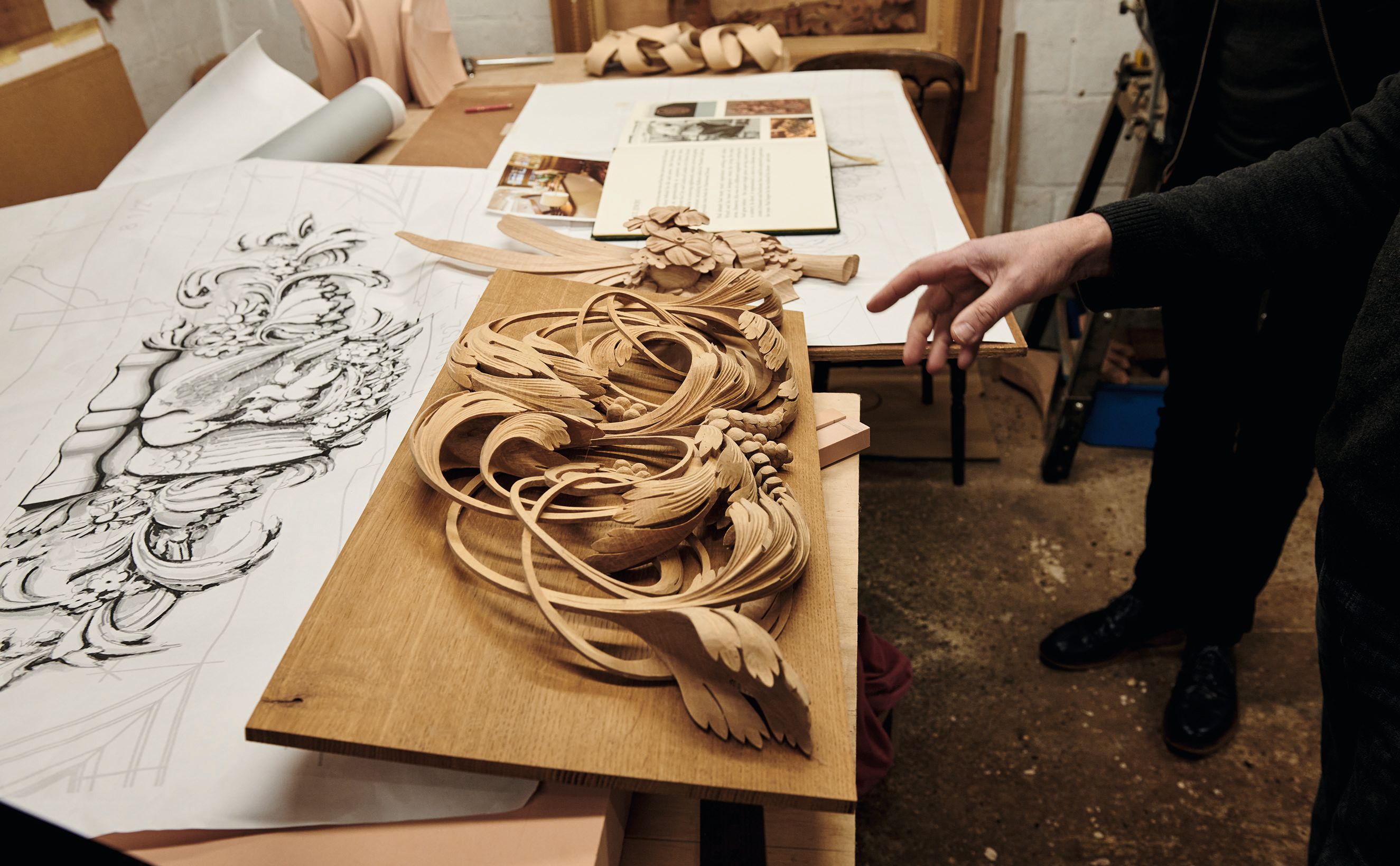
Jewby is not only talented but also enthusiastic about his profession. As a personal challenge, he once tried to make an exact replica of a piece by Grinling Gibbons, an Anglo-Dutch sculptor who is widely regarded as England’s greatest carver of all time.
“I went to Trinity College Library in Cambridge where there’s some of his work, these little scrolling leafworks that entwine in and out of themselves, and I took a measure of the drawings, came back and carved it,” he states. Today, Jewby’s version hangs above his fireplace. “I look at it every day,” he says, “and I like to think Gibbons would have said it’s good enough to go on a job!”
There aren’t, as you might expect, a shortage of carvers in Britain. “What I feel sad about is that there are a lot of them – most people get trained now at City and Guilds Art School in London – and they leave there thinking that they are really good carvers. In fact, a lot of times they’re not,” he says.
“To learn how to use your tools and to cut wood takes two or three years. But to learn what to do, what to cut, what forms to shape, that takes decades. It’s about having the confidence to take that big chisel and whack a great bit off. You can’t be timid,” he adds.
For him, the best thing about the superyacht industry is it allows him to practice his craft to the best of his ability, and for a fair price for his time. “I know that people aren’t going to turn around and say to me, ‘You’ve done too good a job,’ which I’ve had several times before. They want the absolute best; I love that – it’s what I strive for.”
First published in the May 2024 issue of BOAT International. Get this magazine sent straight to your door, or subscribe and never miss an issue.
STATE OF SOLAR
A dive into the details of the A96
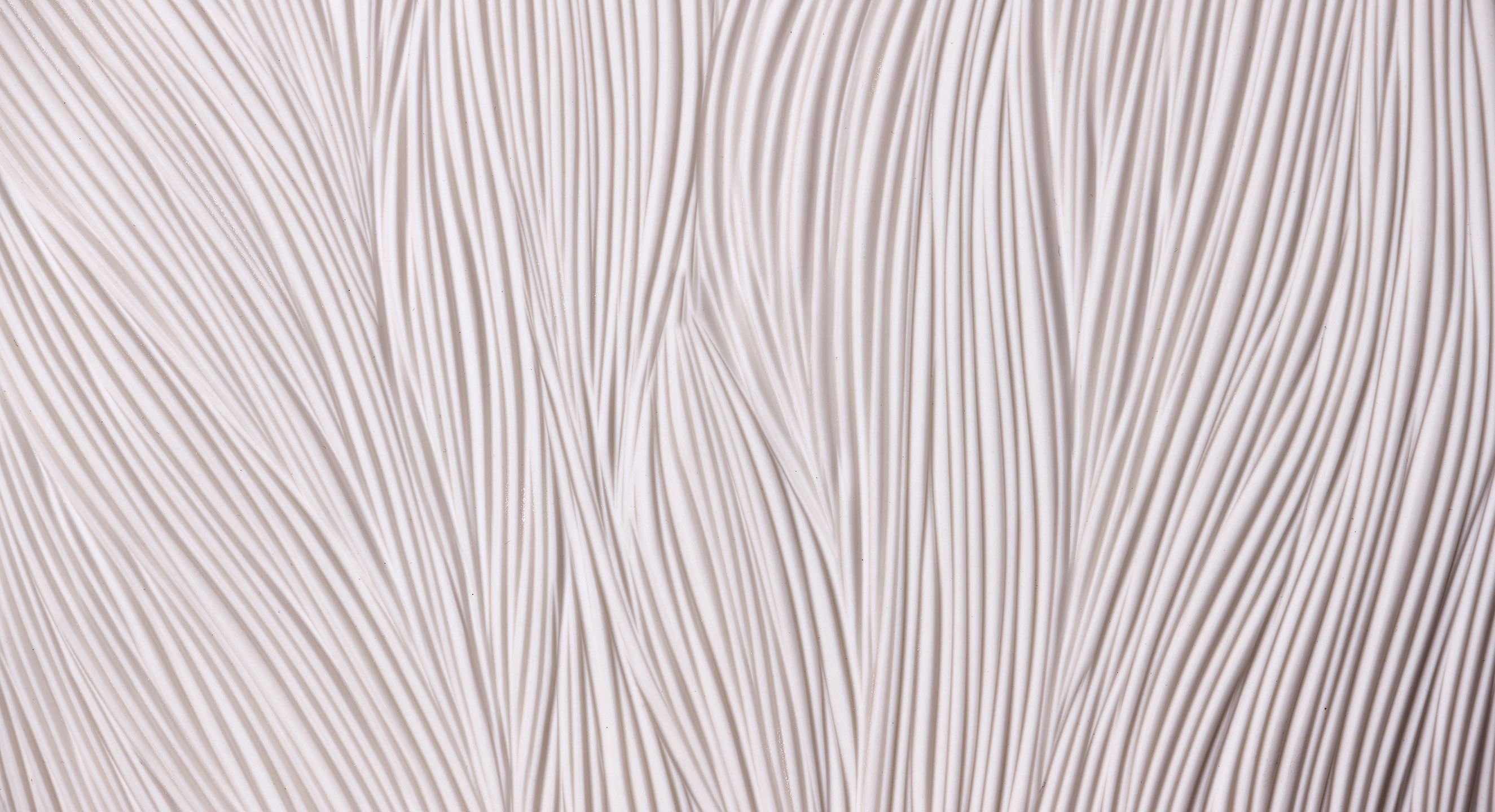
This year’s winners were gifted a fitting trophy for their efforts. Made by luxury materials company Nature Squared, they took four months to make.
“Nature Squared was launched 23 years ago with sustainability front and centre in our minds,” says Lay Koon Tan, the company’s co-founder.
“With craft being the lowest impact manufacturing you can find, as well as nodding to intangibles such as heritage, culture and mindfulness, all of that goes into every single thing that we produce.
“Our mission is to provide the most luxurious, most bespoke, most attractive product possible and keep true to these values.” naturesquared.com
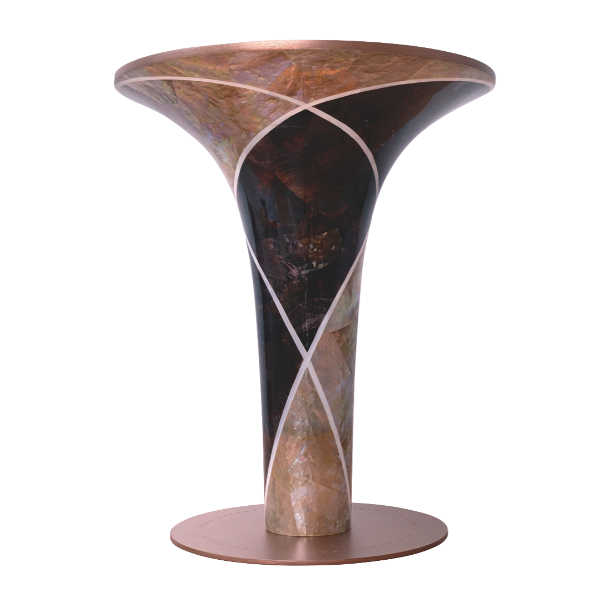